Navigating Operational Excellence: Understanding the Synergy of Lean Manufacturing and Six Sigma
by Gene Kaschak, Vice President
Continuous Improvement & Leadership Development Strategy
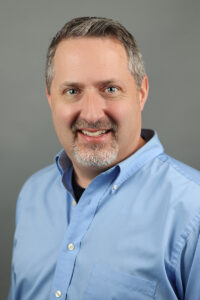
Gene Kaschak,
In the dynamic world of manufacturing, two methodologies shine as indispensable tools for elevating operational efficiency: Lean Manufacturing and Six Sigma. While both share the common goal of enhancing efficiency and minimizing waste, their distinctive approaches set them apart. We’ll explore the nuances that define Lean Manufacturing and Six Sigma, tracing their origins, unraveling core principles, and understanding how their synergy propels organizations toward operational excellence.
Lean Manufacturing traces its roots to the post-World War II era in Japan, drawing inspiration from the Toyota Production System. The primary objective was to eliminate waste and forge a sleek, efficient production system. Conversely, Six Sigma emerged in the 1980s at Motorola, driven by the ambition to reduce defects and variations in manufacturing processes.
Core Principles of Lean Manufacturing:
- Waste Reduction: Lean Manufacturing targets the eight types of waste, encompassing Defects, Overproduction, Waiting, Non-utilized Talent, Transportation, Inventory, Motion, and Excessive-processing. By eliminating these inefficiencies, organizations fine-tune their processes for optimal performance.
- Continuous Improvement (Kaizen): At the heart of Lean Manufacturing is Kaizen, the philosophy of continuous improvement. It fosters a culture where employees at all levels actively engage in identifying and implementing improvements.
- Pull Systems and Flow: Lean operates on a pull system, aligning production with actual customer demand that flows effortlessly through processes with minimal interruptions.
Core Principles of Six Sigma:
- Define, Measure, Analyze, Improve, Control (DMAIC): Six Sigma adheres to the DMAIC methodology, systematically enhancing processes. This structured approach involves defining problems, measuring current performance, analyzing data, implementing improvements, and establishing controls to sustain advancements.
- Statistical Analysis: Six Sigma relies heavily on statistical methods to identify and quantify process variations. This data-driven approach empowers organizations to make informed decisions, reducing defects and enhancing overall performance.
- Focus on Variability: In contrast to Lean Manufacturing’s emphasis on waste reduction, Six Sigma targets the reduction of process variability, striving to achieve consistent high-quality outputs.
Maximizing the Synergy of Lean Manufacturing and Six Sigma:
Companies that are leading in Operational Excellence strategically apply Lean Manufacturing and Six Sigma, leveraging each methodology’s strengths to address specific improvement projects. While Lean exemplifies speed and waste reduction, Six Sigma tackles quality and consistency. Together, they form a formidable alliance, creating a comprehensive framework for continuous improvement. Knowing how and when to apply each methodology is a key attribute of companies sustaining successful continuous improvement programs.
In the coming year, MRC is proud to introduce a Yellow-Belt workshop as part of our Lean Master program. This addition aims to provide aspiring Lean Manufacturing change agents with a foundational understanding of Six Sigma. Armed with this knowledge, individuals will strengthen their ability to drive improvements across a spectrum of challenges in their respective companies. By embracing the principles of Lean and Six Sigma, manufacturers can adeptly respond to market demands, enhance product quality, and stay at the forefront in today’s competitive environment.
About the Author
To discuss Lean Implementation, Lean Coaching, Process Improvements, or Customized Training, please call Gene at (484) 635-4405, or email him at gene.kaschak@mrcpa.org.